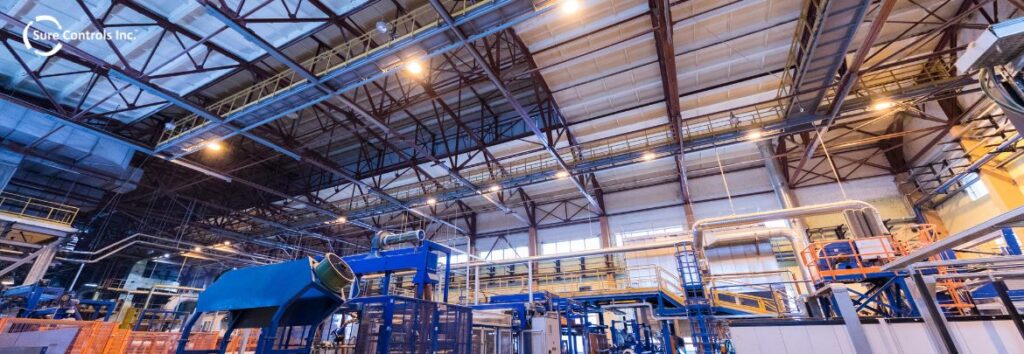
Standalone Temperature Control Components
Temperature control plays a critical role in manufacturing, influencing product quality, energy efficiency, and process reliability. Manufacturers often face a choice between standalone temperature control components—from brands like Watlow, Eurotherm, and RKC—and programmable logic controllers (PLCs) for managing their temperature-sensitive processes. This white paper evaluates the pros and cons of both solutions, focusing on replacement costs, ease of maintenance, upfront costs, and networking capabilities. Additionally, manufacturers must consider long-term maintenance costs when evaluating overall return on investment (ROI), as more complex systems may require skilled personnel for diagnostics and repairs.
Pros:
- Specialized Functionality:
- Designed specifically for temperature control, ensuring high precision and reliability.
- Advanced features such as PID auto tuning, multi-zone control, and alarms are often standard.
- Low Replacement Costs:
- Individual controllers are inexpensive to replace compared to PLC modules. Replace modules with cards
- Availability of drop-in replacements from multiple vendors.
- Simple Maintenance:
- Modular design facilitates quick diagnostics and repairs.
- Often equipped with user-friendly interfaces for local adjustments.
- Incorporating these systems into electrical control panel layouts can further streamline accessibility and serviceability.
- Low Upfront Costs:
- Lower initial investment compared to PLC systems, especially for small-scale or single-zone applications.
- Good Networking and Integration:
- Modern controllers often support protocols like Modbus or Ethernet for seamless integration into supervisory systems.
- They can also be integrated into broader control panel solutions, enhancing communication across equipment and improving overall system visibility.
Cons:
- Limited Scalability:
- Managing a high number of zones or complex processes may require multiple controllers, increasing system complexity.
- Integration Challenges:
- May not integrate as seamlessly with broader manufacturing systems compared to PLCs.
- Space Requirements:
- Each controller occupies panel space, which can become significant in large installations.
Programmable Logic Controllers (PLCs)
Pros:
- Centralized Control:
- Capable of managing multiple temperature zones alongside other process variables.
- Reduces the need for multiple standalone units, simplifying system architecture.
- Advanced Networking:
- Excellent integration with industrial automation networks and systems.
- Supports a wide range of communication protocols and IoT capabilities.
- High Scalability:
- Easily expanded to accommodate additional zones or processes.
- Suitable for complex applications involving synchronized control across multiple zones.
- Long-Term Cost Efficiency:
- While the upfront cost is high, consolidated control can reduce overall system and maintenance costs in large-scale operations.
Cons:
- High Upfront Costs:
- Initial investment in PLC hardware, software, and programming is significant.
- May require specialized programming expertise.
- Complex Maintenance:
- Diagnosing and repairing issues often necessitates skilled personnel.
- Replacement parts for PLCs can be more expensive and less readily available compared to standalone components.
- Overengineering Risks:
- For simple temperature control applications, using a PLC may add unnecessary complexity and cost.
- Redundancy and Backup:
- A PLC failure can impact multiple processes simultaneously, increasing downtime risks.
Comparative Analysis
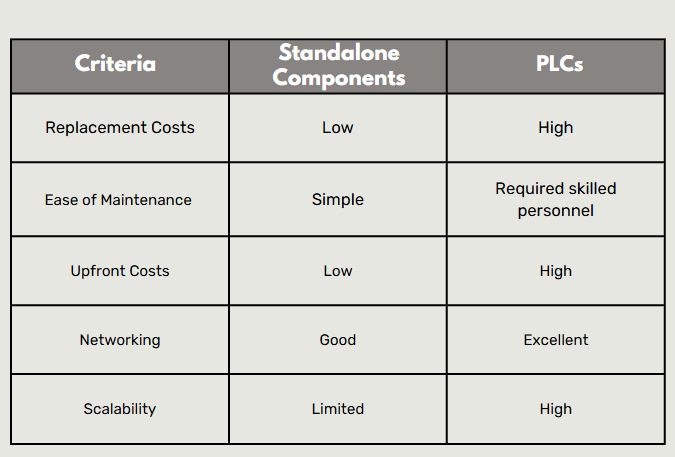
Additional Considerations: Enhancing PLC-Based Temperature Control with Carlo Gavazzi NRG
For manufacturers who prefer utilizing a PLC for temperature control, pairing it with the Carlo Gavazzi NRG series offers additional advantages. By integrating the NRG with PLC-based systems, manufacturers can:
- Reduce Wiring Time: The NRG system simplifies installation and reduces wiring complexity compared to traditional setups.
- Improve Diagnostics: Real-time data monitoring allows for predictive maintenance and minimizes unexpected downtime.
- Enhance Energy Efficiency: optimize power management, reducing energy waste and improving overall system performance.
- Streamline Integration: Ensure a more cohesive and responsive temperature control system.
Conclusion
The choice between standalone temperature control components and PLCs largely depends on the specific requirements of the manufacturing process. Standalone components offer a cost-effective and straightforward solution for simple or localized applications. In contrast, PLCs provide scalability, advanced integration, and centralized control, making them ideal for complex, multi-zone systems. For manufacturers opting for PLC-based temperature control, integrating the Carlo Gavazzi NRG series presents a compelling opportunity to enhance efficiency, simplify installation, and improve overall system reliability. By carefully considering factors such as cost, system complexity, and long-term maintenance, manufacturers can select the best temperature control solution to optimize their operations.